A streamlined component count for an even higher-performance range!
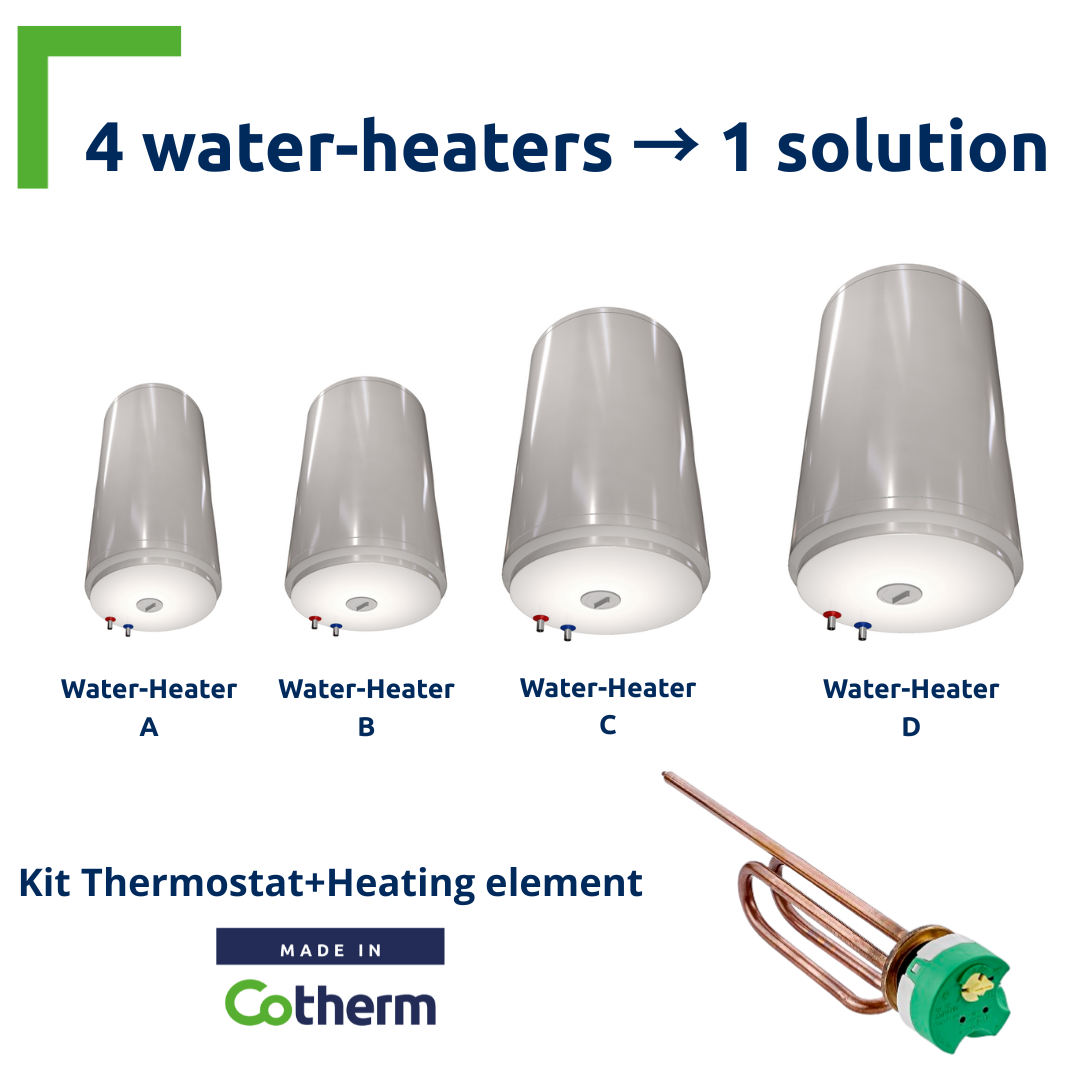
Our customer, a manufacturer of water heaters, wanted to rationalise its range while maintaining compliance with European regulations (ERP Directive 2013/812 and 2013/814) and SASO (SASO 28854:2027). With its existing manufacturing facilities, the new range had to make maximum use of existing facilities and optimise investment.
Key numbers
- 2 models of 30L water heaters, equipped with 1200W resistors of different shapes and 2 different thermostats
- 2 models of 50L water heaters, 1200W and 1500W equipped with 2 different configurations
- Market: several tens of thousands per year
- Project completed in 3 months
The Challenge
- Harmonise the choice of components in the range to optimise supply management and reduce stock
- Guarantee that all production complies with the ERP directive in Europe and Saudi Arabia (SASO)
- As the products are already on the market, the rationalisation of components must not affect the performance of the water heaters.
The solution
Two thermostat + heating element combinations for all water heater models:
- 1 TSX thermostat reference, with Eco point and a 1200W heating element
- 1 TSX thermostat heating element, and a 1500W heating element
Result
By rationalising the solution, it was possible to reduce the number of resistance and thermostat assemblies from 4 to 2, without changing the construction structure of the water heaters.
Cotherm and the thermostat and heating element kit, the advantages
- Expertise in the most appropriate thermostat + resistor configurations for different types of water heater
- Mastery of all the elements: optimising the performance and efficiency of water heaters
- Proposes the best efficiency / performance / product rationalisation alternative by simulating all the possible configurations
- Reduces project times by using high-performance tools (CFD simulation, laboratory tests, etc.) to speed up the process
- Supports its customers from A to Z, from defining the project to marketing the range
The process
Phase 1 : Defining the objectives and characteristics of the project with the customer, such as the schedule, the type of product and the marketing area. Based on these discussions, we draw up a budget.
Phase 2 :We carry out an audit of water heaters, which consists of carrying out a series of tests to establish an initial technical baseline.
Phase 3 : Creation of digital models for CFD simulations. Simulation enables new solutions to be tested, avoiding the prototyping phase. Results can be obtained in less than 24 or 48 hours, depending on the complexity. It also allows us to increase the number of tests, so that we can converge on the best solution through successive iterations.
In our case, we simulated several heating elements shapes and powers to harmonise the 1200W resistor solution: 2 models simulated until we obtained a suitable resistor shape guaranteeing the performance of the V40 and the correct operation of the safety system.
Phase 4 : Following the simulations, samples were taken for validation on water heaters in the laboratory. The laboratory-tested solution confirmed the simulation.
Phase 5 : Once the solutions had been validated by the customer, we moved on to the deployment phase, with the creation of references and the first series production.
Product range
Control, Secure and Heat